The film production process directly affects its performance and quality, and every link needs to be strictly controlled.
Taking OPS film as an example, it usually adopts a biaxial stretching process. During the stretching process, the polystyrene raw material is first heated to above the glass transition temperature to give it a certain fluidity. Then it is stretched at different stretching multiples in the longitudinal and transverse directions, and the stretching multiples are generally between 3-5 times. By precisely controlling the stretching temperature (generally 100-150℃) and the stretching speed, the molecular chains are oriented, thereby improving the strength, transparency and barrier properties of the film. When producing ops high transparant film, the control of the stretching process is particularly critical. Accurate stretching multiples and temperature control can ensure that the film meets the requirements of high transparency. Any slight deviation in any parameters may cause the transparency of the film to decrease.
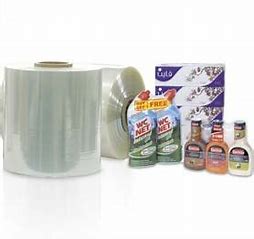
The production of CPP film adopts a casting process, in which the molten polypropylene is cast through the die head onto the cooling roller and quickly cooled and formed. In this process, the control of parameters such as cooling speed and die gap will affect the thickness uniformity and performance of the film. The cooling rate is generally controlled at 5-10℃/s, and the die gap is between 0.5-1.5mm. Only by strictly controlling these parameters can a CPP film with uniform thickness and stable performance be produced.
For aluminized films such as VMCPP film and VMPET film, the aluminizing process is the key. Using vacuum aluminizing technology, aluminum is evaporated and deposited on the surface of the film under a high vacuum environment (the vacuum degree generally reaches 10⁻³-10⁻⁴Pa). The thickness and uniformity of the aluminized layer directly affect the barrier properties and appearance quality of the film. The thickness of the aluminized layer is generally controlled at 30-50 nanometers. By precisely controlling the evaporation rate and deposition time, the aluminized layer is ensured to be evenly distributed.
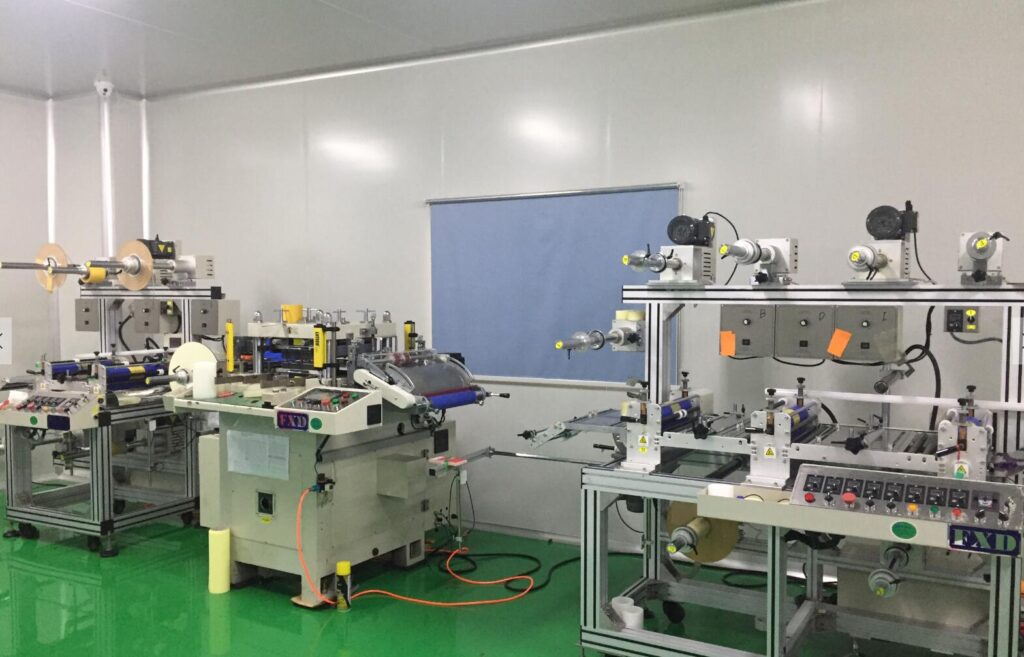
In terms of quality control, every link is crucial, from the selection of raw materials to online testing during the production process to the sampling inspection of finished products. In the selection of raw materials, we strictly screen high-quality suppliers to ensure that the purity and performance of raw materials meet the requirements; in the production process, we use advanced online testing equipment, such as thickness testers, light transmittance testers, etc., to monitor the performance indicators of the film in real time; when sampling finished products, we test the tensile strength, barrier properties, transparency, etc. of the film according to strict quality standards. Only by strictly controlling the quality can we produce film products with excellent performance.